Curso de Técnicas de Impresión 6

Se denominan complejos aquellos productos fabricados a base de combinar mezclas de diferentes materiales.
Según lo expuesto hasta ahora, se puede considerar que están dentro de este grupo los siguientes productos:
a) Autoadhesivos.
b) Metalizados.
c) Extrusionados.
Se describe a continuación, el control de calidad de estos productos.
Se ha visto en capítulos anteriores la fabricación de diferentes soportes de impresión, así como su control de calidad.
En este capítulo se tratarán los diferentes cuidados que deben
observarse con estos soportes, así como también las principales
propiedades que deben tener para un buen comportamiento, tanto en la
impresión como en otras manipulaciones.
Sin duda, los aspectos ecológicos del papel son cada día más importantes, por lo cual se considera conveniente añadir este capítulo.
Ha de señalarse, sin embargo, que se trata de un tema totalmente abierto, ya que la Comunidad Económica Europea aún no ha definido qué es el papel ecológico. Por el momento, existe una comisión de trabajo, pero todavía no ha dado su veredicto.
Por
otro lado, es muy probable que la definición de papeles ecológicos
empiece por productos como los tissues u otras especialidades que no se
hallan propiamente bajo el denominador "mercado de impresión y escritura".
Empecemos por una serie de definiciones para centrar los temas.
Todos
los soportes que hemos tratado anteriormente son comercializados
basándose en nomenclaturas y procedimientos de ensayo normalizados.
Hasta ahora ha sido imposible adoptar unas normas de lenguaje
universal, por lo cual la mayoría de países tienen sus propias normas,
especialmente los más industrializados.
De acuerdo con los diferentes productos, a continuación tratamos las normas más importantes que rigen actualmente.
15.1. Control de calidad de los autoadhesivos
El control de calidad se expone desde dos puntos de vista:
a) Control de las materias primas.
b) Control del producto final.
15.1.1. Control de las materias primas
Se controlan las siguientes características de la lámina y del soporte:
* Gramaje.
* Espesor.
* Lisura.
* Blancura.
* Brillo.
* Carga de rotura o resistencia a la tracción.
* Rasgado.
* Opacidad/Transparencia.
* Humedad relativa.
* Índice Cobb.
* Rigidez.
* Encogimiento PVC.
* Tonalidad.
* Distintos ensayos de impresión (como arrancado, brillo de tintas, microporosidad, etc.)
Estos controles ya han sido descritos anteriormente.
15.1.2. Control de las propiedades del producto final
Las propiedades más importantes que se controlan en los complejos autoadhesivos son los siguientes:
* Fuerza de adhesión.
* Tack.
* Quick-stick.
* Rolling-ball.
* Cohesión.
* Release.
* Envejecimiento del adhesivo.
15.1.2.1. Fuerza de adhesión
Es la fuerza que se requiere para separar una lámina de adhesivo de la placa metálica o de vidrio a la que ha sido aplicada bajo una presión determinada. Dicha separación se lleva a cabo a una velocidad fijada (300 mm/min) y bajo un ángulo también especificado que suele ser 180°, aunque también se mide a 90°.
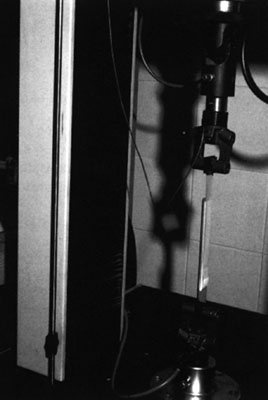
Medida de la adhesión
La adhesión se mide inmediatamente, 20 minutos y 24 horas después de aplicar la lámina a la placa, considerándose la última como la "adhesión final".
De hecho, este ensayo da la fuerza necesaria para romper la unión entre el autoadhesivo y la superficie a la cual se aplica y, dependiendo del valor, se sabe si se trata de un adhesivo permanente o removible y, en definitiva, lo "fuerte" que es el adhesivo.
15.1.2.2. Tack
El tack es la fuerza necesaria para separar un adhesivo de la superficie a la que se aplica, cuando dicha aplicación se ha llevado a cabo de forma rápida, sin presión externa y con un tiempo de contacto mínimo, siendo la presión de aplicación meramente el peso del propio adhesivo.
Esta propiedad es especialmente importante, sobre todo en el adhesivo en bobinas, cuando se trata de aplicación de etiquetas en máquinas automáticas a alta velocidad o, por ejemplo, en la típica pistola de dispensación de etiquetas de precios en los supermercados.
Durante años se ha discutido cómo medir esta propiedad, existiendo en la actualidad varios métodos.
Los dos métodos más ampliamente reconocidos son: el "Quick-stick", adoptado por la FINAT (Federación Internacional de los Fabricantes y Transformadores de Adhesivos y Termoencolantes sobre papel y otros soportes) como oficial, y el "Rolling-ball", también muy difundido.
1) Quick-stick
A una tira de dimensiones normalizadas del adhesivo se le da forma de bucle, con el adhesivo hacia la parte externa, y la parte superior del bucle se monta en las mordazas superiores de un dinamómetro.
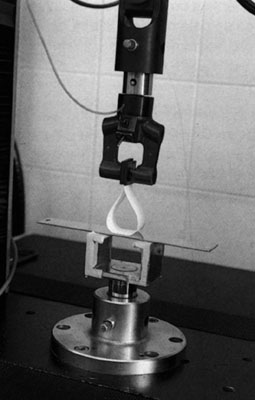
Medida del tack. Quick-stick.
En la mordaza inferior se fija una placa de vidrio o de acero pulimentado. Entonces se pone en contacto el adhesivo con la placa a una velocidad determinada (300 mm/min), hasta que el área de contacto sea de un cierto valor especificado. Inmediatamente se separa el adhesivo de la placa a la misma velocidad. La fuerza necesaria para la separación es el "Quick-stick".
Generalmente se mide sólo en el adhesivo a bobinas, que es el que se utiliza en la aplicación automática. Para aplicaciones manuales el tack es menos importante.
2) Rolling-ball
Se trata de una rampa con un ángulo y longitud determinados, provista de una ranura por la que desciende una bola metálica de dimensiones y peso también determinados. Al final de la rampa se coloca una tira de la lámina de adhesivo a ensayar, con la cara adhesiva orientada hacia arriba. La bola metálica se deja, desde la altura prefijada en la rampa, y se mide la distancia hasta la que llega sobre la lámina. A más distancia, menor tack.
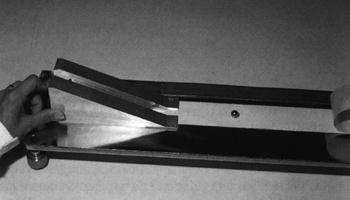
Medida del tack. Rolling-ball
15.1.2.3. Cohesión
La fuerza de cohesión se puede definir como la aptitud del adhesivo para resistir a las fuerzas estáticas tangenciales aplicadas en la misma dirección del plano del que está pegado.
La resistencia a esta fuerza tangencial se evalúa midiendo el tiempo que requiere un peso determinado (1 kg) para causar el desprendimiento de una superficie dada de adhesivo de una placa estándar, en la dirección paralela a dicha placa.
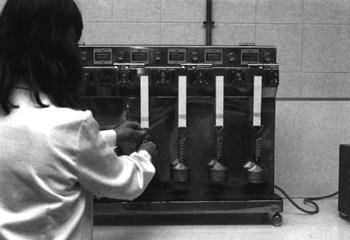
Medida de la cohesión
Este ensayo es muy importante cuando hay que hacer muchos cortes de guillotina, como puede ser el caso de los cromos.
15.1.2.4. Release
El release es la fuerza requerida para separar la lámina de autoadhesivo del papel soporte, medida bajo un ángulo de 180° y a una velocidad de separación determinada.
El valor de esta fuerza debe mantenerse dentro de unos límites determinados, pues si fuera demasiado baja, al fabricar las etiquetas, se caerían por sí solas del soporte y si fuera demasiado alta se desgarraría la malla de la lámina de la que se separa.
Se puede medir el release a baja velocidad (300 mm/min, velocidad de separación entre la lámina y el soporte) o a alta velocidad.
El release aumenta con la velocidad de separación de lámina y soporte. Para que este aumento no sea demasiado acusado, los fabricantes de siliconas experimentan con diversos aditivos para hacerlo disminuir.
Cuando se hacen pruebas con estos nuevos productos, se mide el release a alta velocidad.
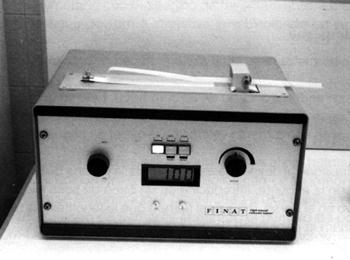
Medida del release.
15.1.2.5. Envejecimiento del adhesivo
La temperatura, el oxígeno del aire y la luz solar (rayos UV) tienen un efecto nocivo sobre el adhesivo, debido a que las cadenas de las resinas y los cauchos se degradan, rompiéndose en cadenas más cortas; lo cual hace descender, con el tiempo, las propiedades de adhesión, tack y cohesión. Además, ocasiona una migración acelerada de las móleculas más cortas de las resinas hacia la parte superior de la lámina, produciendo un agrisamiento de la misma.
Un ensayo para evaluar la resistencia del complejo autoadhesivo a la migración consiste en introducir muestras de una anchura determinada en una estufa a 70 °C y observar el tiempo que tardan en aparecer los primeros puntos de adhesivo migrado en la parte superior de la lámina: cuanto más tiempo, mayor resistencia al envejecimiento.
Se considera que la fórmula del adhesivo es satisfactoria en cuanto a este punto cuando dicho tiempo es mayor a 1 mes.
15.2. Control de calidad del papel metalizado
Los principales controles que se realizan al papel metalizado son los siguientes:
15.2.1. Planeidad
Al estar estos productos metalizados por una sola cara, la planeidad suele ser uno de sus más importantes problemas, por lo que este ensayo es de vital importancia para garantizar un buen comportamiento tanto en la impresión como en el etiquetado.
La planeidad se mide sometiendo el papel metalizado, en una cámara climática, a una elevación de la humedad desde el 55 al 90 %, comprobando su abarquillado.
15.2.2. Resistencia a la sosa
Este ensayo solamente se realiza cuando el destino final del producto es el de etiquetas de botellas recuperables.
El ensayo se hace en un recipiente con una concentración de OH Na al 2 % y a 80 °C de temperatura. Normalmente se mete un trozo de papel metalizado de un tamaño similar a una etiqueta y se somete a agitación. El papel debe aguantar al menos treinta minutos sin romperse.
15.2.3. Facilidad de despegue
Una botella con una etiqueta pegada se introduce en un baño de sosa al 2 % y a 80 °C de temperatura.
La etiqueta debe desprenderse al cabo de 80 segundos. Éste es un ensayo que se realiza para garantizar el despegue de la etiqueta en los baños de lavado de la botella.
Los dos últimos ensayos son también válidos para papel de etiquetas de botellas recuperables sin metalizar.
Una forma de ver la facilidad al despegue es comprobar la prueba de la fenolftaleína. Consiste en hacer una barca con la etiqueta, introducirla en un baño de sosa al 2 % y 80 °C con una cantidad de este reactivo en el dorso y medir el tiempo que la fenolftaleína tarda en colorearse, lo que también determinará la capacidad de traspaso que tiene el papel.
15.2.4. Resistencia a la tracción
Se mide en seco y en húmedo. Para hacer este último ensayo se somete una parte de la tira de papel a un baño de agua durante 2 minutos y luego se mide la carga de rotura (ver medida de la carga de rotura en el papel).
La carga de rotura en húmedo en etiquetas recuperables debe ser como mínimo el 25 % de la resistencia en seco.
15.2.5. Cobb
Se mide sobre el soporte y en el producto final, ya que el lacado puede variar esta propiedad.
Este ensayo ya quedó descrito en el apartado 13.6.
15.3. Control de calidad de extrusionados
Los ensayos sobre los productos extrusionados se concentran en dos partes independientes.
a) Análisis de las materias primas.
b) Análisis del producto final.
Con respecto a las materias primas ya se han comentado los ensayos más importantes, por lo que se trata ahora de describir los controles que se hacen al producto acabado.
15.3.1. Gramaje de plástico
Para hacer esta medida debe separarse el plástico de la cartulina y realizar en una balanza de precisión la pesada correspondiente.
15.3.2. Impermeabilidad al vapor de agua
Se mide sobre muestras sin hender sometidas a un ambiente del 50 % HR y 23 °C de temperatura durante 24 horas. El resultado se expresa en g/m2 y corresponde a la cantidad de vapor de agua absorbido por el complejo.
15.3.3. Adhesión entre la cartulina y el polímero
Puede medirse de la misma forma que el arrancado a la impresión, es decir, en un IGT y evaluando el deslaminado.
También es posible medirlo con el aparato de reventamiento. En este caso, para contrastar el deslaminado, se hace de forma subjetiva; estableciendo un gradiente desde A (muy bueno) hasta D (malo).
Otro tipo de medida para este parámetro sería utilizar el ensayo de resistencia a la tracción.
15.3.4. Ausencia de punto
Se trata de pequeños poros microscópicos que aparecen en la película plástica durante el proceso de fabricación. Son orificios muy pequeños que el ojo humano no puede captar. En la mayoría de los casos, un número limitado de poros carece de importancia. La presencia de poros puede determinarse exponiendo el plastificado a una solución de aguarrás teñida durante un determinado período de tiempo y contando el número de poros que aparece en el reverso del cartón. La presencia de poros se expresa en número/m2.
15.3.5. Tensión superficial
Da una idea de la humectabilidad de la superficie, es decir, indica si la tinta de impresión o la cola se mantendrán sobre la superficie o si se adherirán a ella.
Se expresa en dinas/cm. Generalmente la tensión de una superficie plastificada es demasiado baja para la impresión o el encolado. Por eso la superficie se trata con una descarga de corona eléctrica, como se ha visto en el proceso de fabricación. Esto provoca una ligera oxidación de la superficie que cambia de polaridad, facilitando el anclaje de las tintas y de la cola.
Este ensayo se hace también en los papeles metalizados. Normalmente la tensión superficial recomendada para offset es de 35 dinas/cm, mientras que en huecograbado se recomienda 38 dinas/cm.
15.3.6. Propiedades de termosellado
Se usa una barra con presión variable y una temperatura y tiempo de contacto siempre idénticos. El plástico es termosellado contra un papel estándar o contra sí mismo. Siendo constante la temperatura y la presión, se mide, en segundos, el tiempo necesario para obtener un pegado satisfactorio.
16.1. Recepción del producto
La mayor parte de los productos de los que se ha hablado son soportes celulósicos y debe tenerse en cuenta que la celulosa es un material hidrofílico. Por tanto, dado que los diferentes productos se suministran en unas determinadas condiciones de humedad y temperatura, es muy recomendable que el usuario final no quite el embalaje hasta el momento de usar el producto.
Normalmente los productos celulósicos se suministran con una humedad relativa aproximada del 50-55 % y a una temperatura de 20 °C. Si el papel es sometido a una humedad superior ganará humedad del ambiente y se ondulará, produciendo agujetas en la impresión.
Antes de imprimir, es muy importante que el impresor tenga el producto embalado en el taller durante 24 a 48 horas para que se acondicione. Asimismo, si el papel se imprime en máquina de uno o dos colores el papel debe taparse con plástico entre las diferentes pasadas por máquina. (Ver punto 14.2. sobre humedad).
Al impresor el controlar la calidad del papel no le resultará fácil, ya que los aparatos de laboratorio son muy caros y son difíciles de rentabilizar en una imprenta. Se recomienda, sim embargo, el control de algunos aspectos, tales como la medición de la humedad con el aparato denominado Rotronic y observar la planeidad; también se puede hacer un muestreo de polvillo de corte pasando un trapo de color negro por la superficie del papel y por los cantos de la hoja, etc.
16.2. Características del papel para imprimir en tipografía
Este sistema de impresión está en franca decadencia y, hoy en día, es muy poco el papel que se imprime en tipografía.
Características importantes para la tipografía son:
* Lisura.
* Compresibilidad.
La primera de ellas no es imprescindible, aunque la calidad de impresión mejorará con la lisura. La compresibilidad sí que es más interesante, ya que facilitará la recuperación del papel a su posición primitiva, una vez haya sido sometido a la presión de los tipos.
El producto a imprimir puede ser absorbente o no. En el segundo caso es imprescindible la utilización de tintas completamente oxidativas.
16.3. Características para la impresión en offset
Este sistema de impresión se ha popularizado mucho durante los últimos años, pudiéndose decir que es el más corriente en la actualidad. Se hablará, por tanto, más extensamente de él.
16.3.1. Impresión offset de productos absorbentes
Se incluyen en este grupo los productos que tienen una absorción, bien sea baja, como puede ser la de un papel estucado, bien alta, como un papel sin estucar.
Los productos que corresponden a este grupo son:
* Papeles.
* Cartulinas y cartoncillos.
* Altos brillos blancos.
* Altos brillos de colores tenues.
* Autoadhesivos con cualquiera de las láminas citadas anteriormente.
Aunque en la impresión offset la calidad también mejorará con la lisura del soporte, no es una cualidad imprescindible.
Deberá tener:
* Planeidad (requisito imprescindible).
* No desprender polvillo.
* Microporosidad adecuada para un rápido secado de tintas.
Cumpliendo estos tres factores será ya suficiente. Las demás características como brillo, blancura, etc., ya son atributos a añadir, pero los tres requisitos anteriores son imprescindibles.
Dentro de los papeles con absorción se emplean las tintas de filtración selectiva que secan por penetración y oxidación. Este punto es muy importante porque hay impresores que asocian facilidad de secado de una tinta con facilidad de absorción, y esto no es así, debido a que la oxidación de la tinta será más rápida cuanto más en superficie quede. Ocurre, por tanto, que en un papel sin estucar si se deposita una masa grande de tinta, éste la absorberá con rapidez; sin embargo, su oxidación será lenta precisamente debido a ese exceso de penetración. Este efecto puede producirse también en un papel mate que normalmente es más absorbente que un papel brillante.
Los papeles mates tienen, por otro lado, el problema de resistencia al frote, debido a que al ser papeles poco calandrados son más abrasivos. Es, por tanto, muy conveniente el seleccionar debidamente tintas específicas para este tipo de papel con contenido en ceras suficiente para dar buena resistencia al frote. Por supuesto, la elección de planchas o cualquier otro producto que minimice el consumo de agua será beneficioso para reducir este problema.
Lógicamente el barnizado acrílico en línea suele ser un sistema muy eficaz para mejorar la resistencia al frote.
16.3.2. Impresion offset de productos no absorbentes
Serán productos carentes de poro tales como:
* Papeles metalizados.
* Cartones extrusionados.
* Plásticos en general.
* Acetatos.
* Altos brillos de colores intensos.
* Altos brillos con acabado: Metálico / Madreperla.
En este tipo de productos, al estar totalmente exentos de poro, la absorción de la tinta es imposible; por lo que debe elegirse una tinta que seque exclusivamente por oxidación.
En este caso las condiciones de la máquina son más drásticas, por lo que es recomendable:
* Controlar al máximo el agua de mojado.
* No utilizar pulverizadores.
* Hacer pilas muy pequeñas.
* Utilizar polvos antimaculantes orgánicos.
Un sistema que se emplea para imprimir, en ocasiones, este tipo de productos son las tintas de secado por ultravioleta. En este caso, el secado de la tinta se realiza por reacción química y es inmediato; por lo que será, sin duda alguna, el mejor sistema para imprimir estos productos.
16.4. Características para la impresión en huecograbado
El secado de las tintas de huecograbado siempre es por calor, por lo que la absorción no es importante.
Para poder imprimirse en huecogrbado cualquier producto gráfico deben cumplirse dos condiciones básicas:
* Lisura.
* Compresibilidad.
La primera de ellas es imprescindible. Sin lisura se tienen problemas de ausencia de punto y, especialmente cuando se impriman tramas finas, la calidad obtenida puede ser realmente inadmisible.
La compresibilidad es también importante, pudiendo compensar en algunos casos (quizás más en papeles no estucados) una posibles falta de lisura.
Dado que el huecograbado va normalmente en bobinas, ni que decir tiene que, el buen bobinado del producto a imprimir será también una condición muy interesante para un resultado óptimo de la impresión.
En huecograbado se suelen imprimir revistas y también muchos soportes no absorbentes, debido a que el secado de las tintas es rápido, ya que son tintas líquidas fabricadas con disolventes muy volátiles.
16.5 Características para la impresión en flexografía
Dado que en este sistema de impresión se utilizan tintas de agua, es importante utilizar soportes bien encolados cuando se trata de papel, ya que de esta forma se regula la absorción y se incrementa el brillo de la tinta.
Cuando se trabaja en bobinas, lo mismo que el huecograbado, es muy importante la calidad del bobinado.
16.6. Características para la impresión de fotocopias
Lo más importante en esta impresión es el mantenimiento de la humedad en unas condiciones inferiores a la impresión offset, aproximadamente a un 40 % de HR, especialmente cuando las máquinas son de elevada producción y se imprimen las dos caras. En láser caliente esta humedad es la más correcta.
En fotocopiadoras más sencillas, las condiciones son mucho menos críticas.
16.7. Otros sistemas de impresión
En otros sistemas de impresión las condiciones del papel son menos críticas.
Como norma general puede decirse que cualquiera que sea el sistema de un papel debe ser:
* Plano.
* Dimensionalmente estable.
* No tener desprendimientos de fibras.
* Si se imprime en bobinas un perfil correcto de dureza.
16.8. Ensayos de imprimibilidad
Los ensayos de imprimibilidad se hacen fundamentalmente en aparatos IGT o Pruff-bau, a excepción del ensayo de tinta porométrica y el microcontourtest.
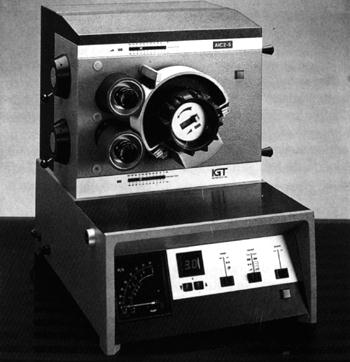
Aparato de ensayos IGT
Los resultados obtenidos tanto con IGT como con el Pruff-bau son bastante similares. Los fabricantes de papel y de tintas suelen disponer de los dos para garantizar al máximo la calidad de sus productos.
Ambos aparatos de ensayo se basan en la utilización de unas tintas estándares que darán una idea sobre el posible comportamiento del papel en la máquina de imprimir en lo que se refiere a secado de la tinta, brillo de ésta, resistencia al arrancado de la capa de estucado, rugosidad del papel, etc.
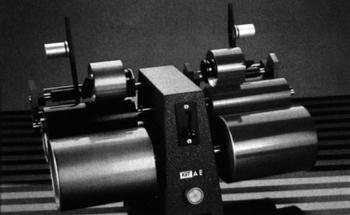
Entintador del IGT
Los ensayos de imprimibilidad siempre se hacen sobre tiras estrechas más o menos de 15 a 30 mm. Esto hace que en ocasiones no se detecten ciertos fallos que luego pueden salir en la impresión. No obstante, debe tenerse algún punto de referencia y en la mayoría de los casos estos ensayos son de una gran utilidad, permitiendo conocer al papelero las posibilidades y los problemas que puede presentar el papel que va a vender.
Los ensayos que se realizan con el IGT o el Pruff-bau son los siguientes:
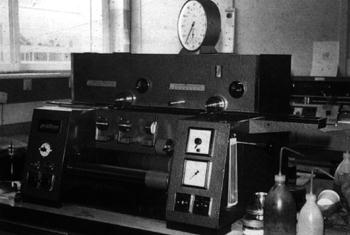
Aparato de ensayo Pruff-Bau
16.8.1. Microporosidad
Este ensayo mide la capacidad de absorción del papel.
Para hacer esta medición se imprime una tira de papel y luego se provoca el repintado con otro papel patrón a diferentes tiempos, concretamente a 15,30 y 60 segundos, pudiendo hacerse si se desea más largos.
En función de la diferencia existente entre las tres partes de la tira patrón se verá si el papel puede repintar o no. La microporosidad de un papel brillante normalmente es inferior a uno mate, es decir, este último será más absorbente.
16.8.2. Arrancado en seco
Con este ensayo se pretende determinar la unión existente entre la capa de estuco y el soporte. El arrancado puede ser sólo de la capa y, en ocasiones, si el soporte tiene una resistencia interna débil, puede llegar a deslaminarse.
Para hacer el arrancado se realizan unas impresiones con aceites de diferentes viscosidades, determinando el lugar donde el papel empieza a arrancar. En función de este lugar se da un valor de arrancado en centímetros/segundo, con lo que se determina si el papel es correcto o no.
El ensayo de arrancado permite, por tanto, ver si la salsa de estucado tiene la calidad adecuada, o bien, si el soporte no deslamina.
Existen, a veces, otros defectos de desprendimientos que no obedecen a una falta de ligante o resistencia del papel, sino que están relacionados con otras circunstancias.
Estos defectos pueden ser los siguientes:
a) Desprendimiento de partículas
Ocurre, a veces, con la fabricación del papel, que por problemas de limpieza u otros motivos pueden quedar salpicaduras de salsa u otras partículas sobre el papel. Si en el escogido este defecto no es controlado (en ocasiones es imposibles si las partículas son blancas), el papel saldrá al mercado y cuando se imprima estas partículas quedarán sobre el caucho de impresión, en el caso offset. Estas salpicaduras no pueden ser detectadas en el IGT, ya que, como se ha dicho, se analiza una tira estrecha de papel y sólo podría verse si se tuviese la fortuna de coger una tira que contuviera alguna partícula.
Este problema sólo se podrá determinar, por tanto, en una máquina de imprimir.
b) Polvillo de corte
A veces, si las cuchillas de bobinadoras o cortadoras no están perfectamente afiladas pueden originar polvillo sobre el papel. Este polvillo estará completamente suelto sobre la hoja y cuando se imprima el papel quedará sobre el caucho, produciendo defectos en la impresión.
Ambos defectos pueden ser solucionados, en ocasiones, en la imprenta; dándole al papel una pasada en blanco, aunque esto tiene su coste.
Estos dos problemas son denominados por los impresores como arrancado. No obstante, es muy importante distinguir cuando es realmente un arrancado auténtico (que obedecería a una formulación incorrecta), o bien, cuando es desprendimiento de partículas, polvillo de corte, etc.
Normalmente siempre que se hacen ensayos de arrancado suelen emplearse dos aceites diferentes. En ocasiones, si se intuyen posibles problemas de arrancado en el papel tales como vasos de eucalipto, que no son detectables con aceites, puede utilizarse un tinta llamada Standard C, que tiene un mayor tiro y los puede llegar a arrancar.
16.8.3. Arrancado en húmedo
Como es sabido, la impresión en offset se basa en la repelencia existente entre el agua y la grasa (tinta). Dado que los ligantes usados en el estucado son solubles en el agua, es preciso insolubilizarlos y se necesita, por tanto, un ensayo que demuestre si la insolubilización es correcta o no.
La insolubilización suele hacerse con resinas de melamina que tardan un cierto tiempo en reaccionar, por lo que este ensayo conviene hacerlo como mínimo 24 horas después de fabricar el papel.
En el caso de que los ligantes no estén bien insolubilizados, el papel puede dar el problema definido como grueso en el caucho, es decir, el agua va arrancando parte de la capa de estuco que queda sobre el caucho y va traduciéndose en una pérdida continua de la calidad de impresión.
Este problema no tiene por qué tener siempre su origen en el papel. En ocasiones, ocurre que si el pH del agua de mojado no está sificientemente controlado y baja a valores muy ácidos, pueden producirse disoluciones del CaCO3 que lleva la capa de estucado.
El ensayo de arrancado en húmedo se hace imprimiendo una tira de papel y poniendo en una moleta una gota de agua desionizada. En función de la estela que produzca esta gota sobre la tira impresa se decide si el papel es correcto o no.
Actualmente los arrancados en húmedo de los papeles suelen ser menos frecuentes que antes. Esto es debido a que las máquinas suelen tener el mojado de agua con alcohol. El alcohol baja la tensión superficial del agua facilitando que ésta moje mejor, lo que permite reducir al mínimo la cantidad de agua.
16.8.4. Brillo de la tinta
Es una forma de ver en la fábrica el posible realce de la tinta sobre el papel. Para hacer este ensayo se imprime una tira del papel a analizar con una cantidad de tinta fija.
Normalmente en los papeles mates se pone más cantidad porque son más absorbentes. Una vez impresa la tira, deben esperarse 24 horas, tiempo durante el cual la tinta se habrá secado y, por tanto, ya no puede penetrar más dentro de los poros del papel.
Cuando la tinta está seca se lleva la tira de papel impresa al aparato medidor de brillo y se comprueba el brillo de la tinta.
16.8.5. Índice de barniz
Es un ensayo que se hace normalmente en los papeles estucados 1/c que, debido a que van para etiquetas, se barnizan habitualmente. No obstante, se puede hacer sobre cualquier tipo de papel.
El índice de barniz se hace utilizando una gota de líquido de color rojo (ftalato de dibutilo). Esta gota dejará una mancha sobre el papel que será más larga cuanto mejor sea la barnizabilidad del papel.
El resultado se expresa por los milímetros de longitud de la mancha impresa. Los papeles brillantes siempre tendrán una mejor barnizabilidad que los mates, ya que éstos son más absorbentes y, por tanto, la estela dejada por la gota en estos últimos siempre será menor.
16.8.6. Rugosidad IGT
Conceptualmente tiene gran similitud al ensayo anterior. Se trata de extender una gota de tinta sobre el papel y comprobar la longitud de la estela.
Cuanto más larga sea ésta, mayor lisura tendrá el papel.
16.8.7. Resistencia al frote
Es un ensayo específico para los papeles mates y semimates. Como se sabe, estos papeles suelen presentar problemas de ensuciamiento en la encuadernación al ponerse en contacto las zonas impresas con las zonas en blanco del papel. El ensayo consiste en imprimir una tira de papel con una tinta roja y esperar 24 horas para garantizar el secado de ésta. Cuando la tinta está seca se frota contra un papel en blanco en un aparato Pruff-bau. En función de la mancha que se produzca sobre el papel estándar se da un valor de resistencia al frote.
16.8.8. Heliotest
Es un ensayo específico de los papeles que han de ser impresos en huecograbado. Como se sabe, en estos papeles es muy importante la lisura superficial.
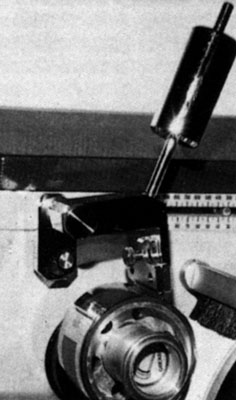
Heliotest
El ensayo se realiza colocando en el IGT una moleta especial grabada en huecograbado. Asimismo, la tinta a utilizar para el ensayo será líquida. Una vez dispuesta la moleta sobre el IGT, se hará la impresión de un tira estrecha de papel.
El sistema de compobar si el papel tendrá o no un comportamiento correcto en la impresión, será medir la distancia existente entre el principio de la impresión y el punto faltante número 20. Cuanto mayor sea esta distancia, mejores condiciones tendrá el papel para la impresión en huecograbado. Es, en definitiva, un ensayo en el que se visualiza la ausencia de punto en la impresión provocada por la falta de lisura del papel, sin duda, uno de los problemas más graves en el huecograbado.
16.8.9. Ensayo de tinta porométrica
No se hace con el IGT.
Es incluído aquí porque es un ensayo realizado para ver las características de absorción de un papel, aunque su resultado es menos fiable que el de microporosidad. Consiste en dejar una mancha de tinta (puede hacerse con el tapón de una botella) y luego quitarlo con algodón, al cabo de diferentes tiempos, viendo la mancha que deja sobre el papel.
16.8.10. Microcontour-test
Es un ensayo para medir la lisura del papel de forma manual. Consiste en aplicar una tinta azul de granulometría elevada sobre el papel. Una vez aplicada, se retira con un algodón. Cuanto menor sea la mancha azulada sobre el papel, mejor será la lisura de éste. En un papel brillante no dejará prácticamente mancha. En uno mate quedará una mancha tenue y en un papel sin estucar la mancha será más intensa.
Este ensayo permite también detectar posibles diferencias entre las dos caras del papel.
17.1. ¿Qué es la Ecología?
Ecología es una palabra derivada del griego (oikos = lugar, casa / logos = ciencia, teoría), y puede definirse como la ciencia que estudia las relaciones entre los organismos y su entorno.
17.2. Polución
Es un cambio no deseado en las características físicas, químicas o biológicas del aire o del agua, que pueden dañar nuestra vida, nuestras ventajas,… o la de las otras especies.
17.3. Elementos polucionantes
Son residuos que producimos y que desechamos. La polución aumenta no sólo porque aumenta la población, sino porque también aumenta el consumo y porque el espacio para cada persona es menor, ya que se generan muchos residuos. Como la Tierra está superpoblada, podemos decir que la papelera de una persona es el espacio para la vida de otra.
Considerando la producción del papel, antes de valorar el posible impacto ecológico que genera, se ha de definir qué es un ecobalance.
17.4. Ecobalance del papel
El ecobalance es un objetivo, descripción cuantificada o necesidades de energía, materias primas, emisiones de aire, efluentes, residuos sólidos u otros productos emitidos durante el ciclo de vida de un producto o durante un proceso o actividad. En pocas palabras, y pensando en el papel, tenemos:
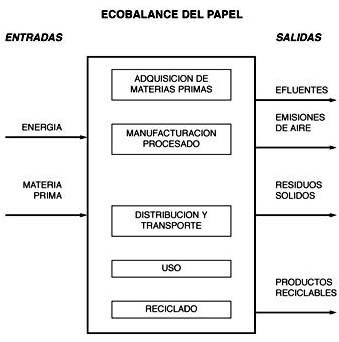
Ecobalance del papel
Es decir, por un lado observamos que para fabricar papel necesitamos unas materias primas y energía, pasando por una fase de producción, conversión y reciclado, y generando unos efluentes líquidos, unas emisiones de aire y una serie de residuos sólidos.
Cuando establecemos la ecología de un producto es indispensable considerar su ciclo de vida. Si nos fijamos en el ciclo de vida del papel, vemos que es completamente cerrado. Parte de una materia prima, se fabrica y el producto final puede ser reciclado después de usarlo. Por otro lado, el papel puede ser incinerado con un mínimo impacto medioambiental y es biodegradable, transformándose en carbono, oxígeno e hidrógeno. Cuando se quema desprende CO2, que puede ser consumido por los árboles. Los productos papeleros también pueden ser utilizados como fertilizantes.
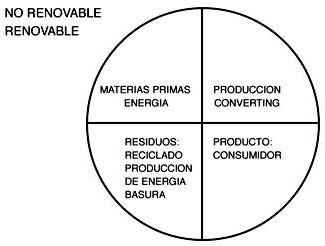
Ciclo de vida del papel
Cuando hablamos de ecología, por tanto, se han de considerar las diferentes fases del ciclo de vida del papel. De acuerdo con esto, los puntos más importantes son:
* Suministro de madera.
* Producción de pasta.
* Producción de papel.
* Reciclado.
17.5. Suministro de madera
Cuando se habla del papel como producto derivado de la madera, la primera cuestión que surge en la calle es: ¿cuándo se acabarán los árboles? Evidentemente, la pregunta contiene un profundo desconocimiento sobre la materia, ya que, sin duda, las industrias papeleras son las que llevan a cabo más repoblaciones. Si no fuese así, estarían condenadas a desaparecer. Estas repoblaciones sirven, entre otras cosas, para la eliminación de CO2 de la atmósfera, con lo cual es posible reducir el efecto invernadero que, sin duda, es uno de los aspectos más preocupantes del medio ambiente.
La madera está compuesta prácticamente en su totalidad por carbono, oxígeno e hidrógeno. En un bosque natural los árboles que no son talados acaban muriéndose, por lo cual parece lógica la manipulación de la madera para transformarla en productos como la pasta y el papel, entre otros. Como ya hemos dicho antes, con la reforestación, el hombre hace que el CO2 liberado en la mayoría de procesos energéticos o en la descomposición de productos papeleros pueda volver al bosque con la ayuda de la energía solar. Este ha sido, es y será el ciclo de funcionamiento de la naturaleza.
Por otro lado, la industria papelera no es la única que se beneficia de la transformación de la madera. Existen otras industrias, como la de la construcción o la del mueble, que son consumidoras de una cantidad importante de este producto, con la particularidad de que consumen las partes de más calidad, lo cual probablemente mucha gente desconoce.
Esto hace que las grandes compañías papeleras se integren formando su propia industria de tableros, gastando actualmente la madera de más calidad. Los residuos de estas fábricas también se utilizan en la fabricación de pasta, igual que los árboles procedentes de los clareos de los bosques.
El incremento de las masas forestales en países como los nórdicos, con una dura climatología que hace que el crecimiento del árbol sea lento, es el ejemplo más claro del hecho de que un bosque bien gestionado y tratado puede incrementar sus recursos.
Esto no ha de confundirse, sin embargo, con la deforestación que sufren las selvas tropicales a causa de la necesidad de utilizar la madera como energía y de disponer de mayor espacio de cultivo para la supervivencia de un gran número de personas que viven en una situación precaria.
17.6. Producción de pasta
En los capítulos 4 y 5 ya hemos hablado de los tipos de pasta que hay, por lo cual no es necesario volver a repetirlo. Sin embargo, es importante tener en cuenta el sistema de blanqueo, ya que es en este punto donde el papel es ecológicamente más cuestionado.
Recordemos que el blanqueo de la pasta es necesario porque en la cocción la madera queda de color oscuro, especialmente en el sistema kraft.
Por otro lado, el blanqueo es necesario para:
* Limpiar la pasta y el papel de compuestos que causan olor y sabor.
* Limpiar la pasta y el papel de partículas que no son fibras.
* Incrementar la blancura y la imprimibilidad del producto final.
* Incrementar la resistencia del papel contra el envejecimiento, cambios de color y la destrucción mecánica o química.
Por tanto, el hecho de blanquear no implica únicamente fabricar un papel más adecuado, sino también eliminar sustancias no deseables.
Tal y como se ha especificado en el capítulo 6, el blanqueo más clásico a lo largo del tiempo fue mediante la utilización de cloro gas. Actualmente han surgido nuevas tendencias como resultado de la gran inversión realizada por las fábricas de pasta y papel.
Desde el punto de vista ecológico, el cloro gas y, a veces, sus derivados son cuestionados. Las discusiones sobre el cloro gas se basan en la formación de organoclorados. Sin embargo, en una fábrica de pasta kraft, del 100 % de cloro consumido en el blanqueo un 90 % se convierte en sal común y un 10 % en organoclorados. De este 10 %, hay un 90 % de peso molecular alto y un 10 % de peso molecular bajo que representa un 1 % del total.
Si blanqueamos con cloro gas un 10 % de estos productos se convierten en grasas de peso molecular bajo, mientras que el 90 % pasan a ser productos solubles en agua no tóxicos. Si utilizamos dióxido de cloro el 100 % se convierte en productos de peso molecular alto solubles en agua.
En resumen, si blanqueamos con cloro gas la obtención de productos altamente clorados es de un 0,01 % del total, y, por tanto, completamente inocuo.
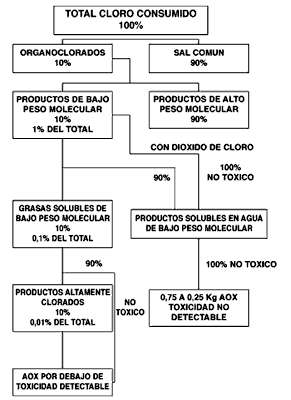
Estructuramos la exposición anterior en un diagrama de bloques con la finalidad de hacerla más fácilmente comprensible.
Otra de las observaciones que se suelen hacer es la presencia de dioxinas. Las dioxinas son derivados clorados. Hay más de 200 tipos de dioxinas diferentes. Sin embargo, se ha demostrado que el porcentaje de dioxina en una industria papelera es extraordinariamente bajo e inocuo.
A pesar de ello, la industria papelera va eliminando el cloro gas de sus procesos de blanqueo. El sistema de blanqueo, actualmente va evolucionando hacia dos tendencias:
1ª Tecnología ECF (Elementary chlorine Free)
Se trata de una tecnología en la cual se blanquea sin cloro gas, pero se utiliza el dióxido de cloro. La defienden grandes compañías americanas que piensan que el dióxido de cloro no es contaminante.
2ª Tecnología TCF (Totally chlorine Free)
En este caso no se utilizan derivados del cloro. Se suele utilizar oxígeno, agua oxigenada y ozono.
Esta tecnología se ha propagado fundamentalmente por los países nórdicos europeos. Según los norteamericanos, los costes que genera la utilización de esta tecnología no son justificados, debido a que las ventajas medioambientales que se obtienen son escasas frente a los costes del ECF.
A continuación damos algunas definiciones importantes en relación a la ecología.
17.7. TOCL
Cantidad total de compuestos orgánicos ligados al cloro. Como en el caso del AOX, da una representación de la cantidad total de compuestos clorados orgánicos en el efluente. No da información sobre los elementos polucionantes que contiene individualmente. El TOCL en el efluente de las plantas de blanqueo es siempre un poco inferior al valor del AOX.
17.8. AOX
Compuestos orgánicos halogenados absorbidos. Aunque hasta ahora se ha dado mucho valor a este parámetro, empieza a haber ciertas discusiones sobre su validez, por las razones siguientes:
* Es la suma de una serie de parámetros que incluyen una mezcla de componentes.
* Estudios recientes han demostrado que el AOX no está relacionado linealmente con los efectos biológicos y ecológicos.
No obstante, es un parámetro que hasta ahora ha servido de guía a las fábricas de pasta que quieren dar una imagen de preocupación por el medio ambiente.
17.9. DQO
Define la totalidad de compuestos orgánicos que contiene la sustancia efluente. Es, en definitiva, la demanda química de oxígeno.
17.10. DBO
Es la demanda biológica de oxígeno. Está relacionada con la cantidad de componentes orgánicos que contiene la sustancia efluente, es decir, será mayor cuanto más producto orgánico haya.
En los efluentes de las fábricas, estos parámetros son medidos juntamente con las emisiones de gases sulfurosos, y, seguramente, la etiqueta ecológica (ecolabel) irá de acuerdo con los valores obtenidos.
La AOX es un dato específico de las fábricas de pasta, mientras que el DQO y las emisiones de azufre también pueden ser medidas en fábricas de papel no integradas.
17.11. Fabricación de papel
En la fabricación de papel no hay un impacto ecológico realmente importante, siempre que las aguas residuales sean convenientemente depuradas.
Tanto en la fabricación del papel como en la de la pasta se están realizando esfuerzos importantes que van dirigidos en tres direcciones.
* Reducción del consumo de agua. Así, por ejemplo, mientras que en los últimos cinco años la fabricación del papel prácticamente se ha duplicado, la cantidad de agua consumida se ha dividido por diez.
* Una mejora en las emisiones aéreas. Los trabajos de recuperación de energía cada vez son más frecuentes.
También el fuel va siendo sustituído por el gas natural, para reducir las emisiones de azufre.
* Un mejor control del proceso de producción, que implica una reducción de las mermas y, en consecuencia, el mejor aprovechamiento de las materias primas.
En definitiva, el papel necesita aire fresco, agua limpia y madera buena. Es evidente que los papeleros son los primeros interesados en mantener estas constantes, para hacer más viable su proceso. Dentro de la fábrica de papel, las inversiones primordiales van dirigidas al ahorro de energía, poniéndose para ello en marcha numerosos programas de cogeneración.
17.12. Papel reciclado
Tal y como ya se ha dicho, se trata de un papel producido a partir de fibras secundarias, es decir, que ya han tenido al menos un uso. La ecología en la producción de este tipo de papel irá relacionada también con el control de los vertidos y de los residuos sólidos. No hay duda de que en la operación de reciclado hay fases, como la de selección de materias primas o el destintado, que obligan a llevar un buen control para evitar impactos medioambientales.
El contenido de fibras secundarias de un papel puede ser variado. No obstante, a falta de definiciones estandarizadas, podríamos decir que para considerar un papel como reciclado ha de llevar como mínimo un 50 % de fibras secundarias.
A pesar de que mucha gente dice que todo el papel tendría que ser reciclado, hemos de decir que esto es imposible por las razones siguientes:
* No todos los papeles pueden ser reciclados, por ejemplo: tissues, libros de alta calidad.
* Las fibras no pueden ser recicladas de forma indefinida, el uso ideal sería de 3 a 5 ciclos.
* Hay usos, como la alimentación, en los que no es aconsejable la utilización de fibras secundarias.
En definitiva, hay un axioma que no admite ninguna duda: no puede haber papel reciclado sin papel fabricado con fibra virgen.
Por tanto, los fabricantes de papeles con fibra virgen y con fibras secundarias han de tener en cuenta que ambos papeles son complementarios. Los primeros son los proveedores de los segundos y estos colaborarán con el reciclado en el mejor aprovechamiento de una materia prima y, sin duda, en la reducción de los residuos sólidos.
Por tanto, no es lógico que mucha gente clasifique como ecológico nada más el papel reciclado.
17.13. Conclusiones
Para acabar este capítulo, resumimos brevemente los diferentes puntos que hemos tratado:
* El fabricante de pasta y de papel no practica la deforestación. Al contrario, planta muchos más árboles que no tala. Es la única forma de asegurarse la materia prima y, en definitiva, su futuro.
* Las inversiones realizadas por la industria papelera en investigación y mejoras medioambientales son muy elevadas. Asimismo, tiene la vocación de seguir en esta línea, animada en conseguir un producto que tenga un efecto medioambiental aún menor.
* Siempre es importante dar informaciones ciertas en los temas ecológicos, ya que, además del valor científico, es muy importante el factor psicológico.
* La integración pasta-papel es en sí ecológica, ya que facilita el mejor aprovechamiento de la energía.
* Es interesante aumentar la recogida del papel. No obstante, el papel reciclado se utiliza específicamente para unos determinados usos finales y es totalmente absurdo decir que el futuro reside exclusivamente en este tipo de papel. El consumo de papel reciclado se incrementará, pero de forma paralela al del papel fabricado con pasta virgen.
* En definitiva, los futuros mercados serán ganados por aquellos que sepan producir con mayor número de recursos y energías renovables, con la mínima polución y que sepan sacar provecho de todos estos aspectos en el desarrollo del producto y en el márketing.
18.1. Normas para papel y cartón
En España son utilizadas las normas UNE (Una Norma Española). Otros tipos de normas utilizadas son las TAPPI (Asociación Técnica de la Industria de la Pasta y el Papel), que son americanas, o bien, las de la Organización Internacional de Normalización (ISO).
Hay también otros tipos de ensayos, normalizados por las mismas casas que fabrican el aparato de análisis.
A continuación citamos las normas más importantes que rigen para el papel y el cartón.
Determinación del gramaje UNE 57014
ISO 536
TAPPI T410
Determinación del espesor y el índice de volumen específico UNE 57004
ISO 534
TAPPI T411
Determinación de las cenizas UNE 57050
ISO 2144
TAPPI T413
Absorción de agua Cobb UNE 57027
ISO 535
TAPPI T441
Resistencia a la rotura por tracción UNE 57028
ISO 1924
TAPPI T404
Resistencia a la rotura por tracción en húmedo UNE 57030
ISO 3781
TAPPI T456
Resistencia al estallido UNE 57058
ISO 2758
TAPPI T403
Resistencia al desgarro UNE 57033
ISO 1974
TAPPI T414
Ceras Dennison UNE 57088
TAPPI T459
Determinación del Scott (Resistencia en la dirección Z)
TAPPI T451 UNE 57075
ISO 2493
TAPPI T489
Lisura Bendtsen UNE 57088
ISO 2494
Lisura Beck UNE 57093
ISO 5627
TAPPI T479
Porosidad Bendtsen UNE 57066
ISO 5636/3
Porosidad Gurley UNE 57065
ISO 5636/5
TAPPI T460
Determinación del brillo del papel UNE 57132
TAPPI T480
Determinación de la blancura UNE 57062
ISO 2470
Determinación de la tonalidad
TAPPI 577
Determinación de la opacidad UNE 57063
ISO 2471
TAPPI T519
Determinación del blistering
TAPPI T526
Rugosidad IGT UNE 57067
pH del papel UNE 57031
ISO 6588 TAPPI T435
18.2. Normas para el autoadhesivo
Las normas más importantes para este producto son las FINAT (Federación de Adhesivos y Termoencolados sobre Papel y otros Soportes). Los números de estas normas son los siguientes:
FTM 1 Adhesividad sobre acero, polietileno, madera, kraft crudo, etc.
FTM 3 Medida del release a velocidad baja.
FTM 4 Medida del release a velocidad alta.
FTM 8 Cohesión.
FTM 11 Pérdida de la adhesividad.
Warning: Use of undefined constant type - assumed 'type' (this will throw an Error in a future version of PHP) in /home/improvisa_com/web/improvisa.com/public_html/wp-content/themes/grassland/comments.php on line 38
Pedazo de noticia, por lo menos larga lo es 😉
Mil gracias Rula y además sabiendo como estas 😉